How to get your music album pressed to a vinyl record in Australia
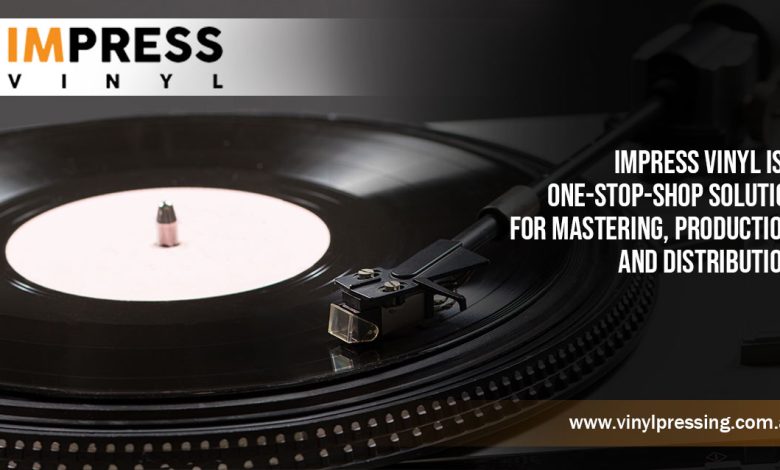
Having your albums on vinyl is undoubtedly worth it in the immediate and in the long run. Custom vinyl pressing in Australia is getting popular again in 2022, with the highest vinyl record sales.
No wonder audiophiles love the old-fashioned way to listen to music rather than online streaming services on their smartphones.
Producing vinyl records in Australia is not more straightforward than you think; musicians and engineers work together to release their favourite albums on vinyl.
While there are a lot of excellent pressing plants still operating around the world, Impress vinyl in Australia predominantly worked with music industry giants to small local businesses in pressing their music on vinyl.
Whatsoever the case may be, if you’re here, you’re probably looking for information on how to press a record. Here are some known tips for making the process fast and effortless.
Reach out to us
How long does it take to press your album on vinyl?
Custom vinyl records in Australia are a fantastic physical product for artists and bands to contribute to their fan base. Having your songs on vinyl could up your game in quite a few ways.
If you plan your schedule and timeline, Impress media has impressive fast lead times that can deliver your vinyl record in four weeks. But as per your customisations and test press options, it can go for six or eight weeks.
Make your vinyl by choosing Impress’s custom vinyl pressing in Australia, with customisations for different labels, designs and packaging for 12″, 10″ and 7″ vinyl records. Also, we offer free 100 CDs in printed card sleeves with every vinyl project order placed.
Custom vinyl masters preparations
Are you preparing to do a custom vinyl records release? Pay special attention during the mix and master the high and low-end content of the material. Do not use frequencies that are below 40hz. Use high pass filters on tracks when mixing to keep these frequencies under control.
The resultant audio is then sent off for mastering, which is the process of preparing the album for reproduction. Mastering vinyl requires special knowledge of the format and a trained ear. A perfectly mastered customised vinyl record has its warmth and depth that will immediately distinguish it from its digital counterpart.
On the other hand, a badly mastered record can cause a turntable’s stylus to track poorly in the record’s grooves, causing unwanted distortion. It can even skip if the sonic errors are too heinous.
Implant media is a custom vinyl record maker in Australia popularly known for fast turnarounds vinyl record pressing while minimising any risk.
Use the highest quality audio format
Like digital formats, custom vinyl pressing can reproduce the entire audible frequency spectrum, but how vinyl achieves this is quite different from how it works in the digital domain. Because a needle has to track the sound waves inscribed in the grooves physically.
The lower the frequency, the wider the groove. If the sound transmitted directly to the groove unaltered, the grooves would have to be excessively wide to adjust all the bass content, shrinking the record’s side and possibly making it unplayable.
Use the highest quality file format that you can. Most pressing plants use 16bit, which is sufficient, but 24bit sounds better to many people.
Stay away from .aiff files. Much online streaming audio software export what they call a .aiff file, but it is not a pro-standard file. Your most beneficial format is to choose .wav files if possible.
Do not overlook the side lengths of a record
The mastering engineer sets a blank lacquer onto the lathe in the vinyl cutting studio. The machine converts the acoustic energy of the recording into the physical motion of a needle on the lacquer.
The lathe is the opposite of a turntable, turning sound into movement instead of movement into sound. The needle tipped with a helium-cooled sapphire or diamond cutting head, the lathe’s needle engraves the music in a single, unbroken spiral looping into the centre of the platter.
The length of one side on a record will dramatically affect the final sound. Depending upon the type of music involved, here are some general limitations:
- 7-inch record with 33 1/3 RPM ideal limit is 6 minutes per side.
- 7-inch record with 45 RPM ideal limit is 4.5 minutes per side.
- A 12-inch record with 33 1/3 RPM is ideal for 18 minutes per side, but 20 minutes per side is still good and 22 minutes per side is generally the max.
- A 12-inch record with 45 RPM is ideal for 12 minutes per side, but 14 minutes is good and 15 minutes per side is generally the max.
Setup your art files preparation
Are you still stuck on your design or didn’t quite know how to set up print-ready artwork? Our talented graphic design team will get your project unstuck and across the finish line.
We are ready to create your custom vinyl records in Australia by helping online or walk-in into our studio for suggestions from our skilled in-house designers.
Customise your vinyl record label, jacket, sleeve, and packaging, always printed at 300 dpi resolution. If you’re printing full-colour art, be sure to use CMYK mode, not RGB.
Using our proper templates helps too, but remember not to embed template lines into your art, or it will only create delays. Download our PDF templates to help you put together the artwork.
Our templates page has PDF versions of all the artwork you need to complete your custom vinyl records. Once completed can be uploaded with your order to be checked and approved by our art department.
Looking for a fantastic vinyl record?
With 20+ years behind us, we’ve printed for labels, artists and musicians in Australia, New Zealand, and across the world. Impress vinyl worked with large corporate clients, professional marketing houses, educational institutions and community groups.
Impress vinyl produces eye-catching vinyl stacks with different colours and combinations. We love to work on your next project with low minimums at cost-effective prices, delivered all around Australia and then onto the world.